Training: The Backbone of Chemical Hygiene Plans
This fourth blog of our EHS and compliance training deep-dive series analyzes chemical hygiene plan (CHP) training importance and key elements.
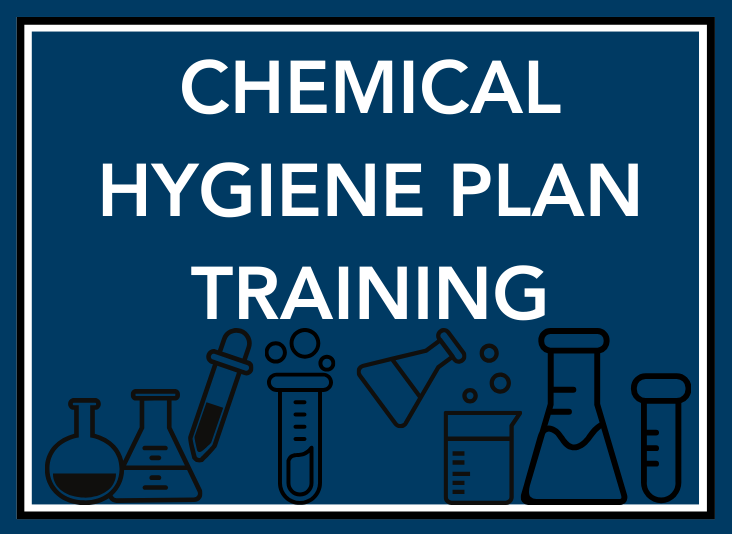
The importance of maintaining a thorough chemical hygiene plan (CHP) is nothing new in the environmental, health, and safety (EHS) industry. Few, however, actually understand the importance of training to it—which is problematic because, as with many safety and compliance programs and solutions, a CHP is only useful if those affected actually know how to use it.
And make no mistake, top chemical hygiene programs are a must in the several hundred thousand facilities that use, store, or manufacture highly hazardous chemicals. In fact, chemical incidents occur approximately every other day in the United States, according to a recent study from the Coalition to Prevent Chemical Disasters. CHPs can help mitigate this—if employees are properly trained to them.
OSHA: The Muscle Behind CHP Training Enforcement
CHPs are crucial: They enable mitigation and response by both internal staff and response crews in the face of the dangers of workplace hazardous chemicals. Mishandling of any hazardous material can cause a chemical event, injury, or other catastrophe—and improper training leads to errors of operation and execution, including in the form of spills, leaks, or fires.
The governing regulation that outlines CHP guidelines is the Occupational Safety and Health Administration’s (OSHA’s) “occupational exposure to hazardous chemicals in laboratories” standard (1910.1450), commonly called the OSHA lab standard. Soon after any chemical incident, OSHA will be knocking on the door to see what went wrong—and potentially impose fines of up to $16,131 per violation, per day. Not only that, but local first responders can enforce the rules at their discretion—as their own and their community’s well-being is at stake.
Due to the prevalence of hazardous chemicals and the frequency with which incidents occur, failure to comply with safety guidelines can result in:
- Worker injury or death
- Risk to the surrounding community
- Operational disruption
- Citations and fines
- Loss of brand image
As such, compliance with this standard is crucial for healthy:
- Employees
- Communities
- Ecosystems
- Finances
As such, training to this plan is essential—to ensure it is carried out as diligently as possible. Fortunately, federally regulated CHP training can ensure employees understand their facility’s written CHP and better ensure lab safety for a facility as a whole. As such, CHP training is the fourth stop on our EHS compliance training deep dive—let’s dig into it more below.
All Entities Need a CHP—And Training
The OSHA lab standard applies to any business or entity that uses hazardous chemicals, and stipulates that they must have a written document that covers hazardous chemical:
- Handling
- Storage
- Use
- Disposal
It also demands there be clearly defined processes and procedures for emergency response or exposure mitigation. Basically, this comes down to:
- What is on site
- How much is on site
- The minutiae of each individual element of hazardous waste at your facility
For further details about CHP requirements, see OSHA’s “Laboratory Safety Chemical Hygiene Plan” fact sheet.
Training Vital for CHP Usefulness
Training is an essential part of a CHP program—because a plan is only good if people actually follow it. Under the OSHA lab standard, training must be:
- Applicable from person to person, for employees who will handle any kind of hazardous chemical. This can include:
- Lab personnel
- Managers
- Facilities personnel
- Custodial staff, if brought into lab spaces to clean up any amount of chemical
- Held at the time of employee hire and annually thereafter
- Hosted any time there is a large or significant change in the CHP—such as:
- After a facility move
- When new materials are brought on site
- During organizational growth or evolution
Training should outline:
- What hazardous chemicals an employee may be exposed to
- Applicable exposure limits
- Health hazards of workplace chemicals
- Exposure signs and symptoms
- The location and availability of reference materials, including instructions about how to access them
- Who the responsible personnel are if there is concern or if a chemical incident were to occur, such as the chemical hygiene officer (CHO) or the emergency response coordinator
- Hazard control measures to minimize exposure (like personnel protective equipment (PPE))
- Methods to detect the presence or release of hazardous chemicals
- All applicable CHP details
Training does not outline how to make and enforce a CHP. All of the aspects that should be covered in training will also of course be in the CHP, but this is not a time to create the plan. Training only covers what the plan is, what it does, and any relevant points. That said, it is important to make sure that the plan itself is correct and thorough before anyone is trained to it.
Custom CHP Training Makes the Difference
Because every organization—in fact, every facility—differs, each CHP (and thus, its training program) will vary slightly as well—down to the small details. As such, a customizable and adaptable training program is necessary for truly effective trainings.
Such a training program should allow for personalization, providing maps of specific facilities and exact details about chemical or emergency response tools and strategies. This way, both internal and external responders will be able to react in an informed way with exact information about the space. This training program should also reproduce the real environment as much as possible, including listing the appropriate internal points of contact with updated pictures and contact information.
Triumvirate Environmental can provide such a training with EHSLearn™: Custom. This unique program offers full CHP training customization—in a way that maximizes learner retention and, thus, safety. We also regularly help create CHPs for our clients—so we can put best practices into a written document on the back end and then help train your employees to it on the front end. Want to learn more? Contact us today.