VOC Emissions at Waste Collection Areas Are Putting Your Lab Staff at Risk
This blog is a supplement to our comprehensive VOCLok Mini-Guide. Here, we discuss the need for a comprehensive solvent waste management solution to both keep employees safe and keep your site in compliance. See the guide and/or the product cutsheet for more information about the VOCLok product.
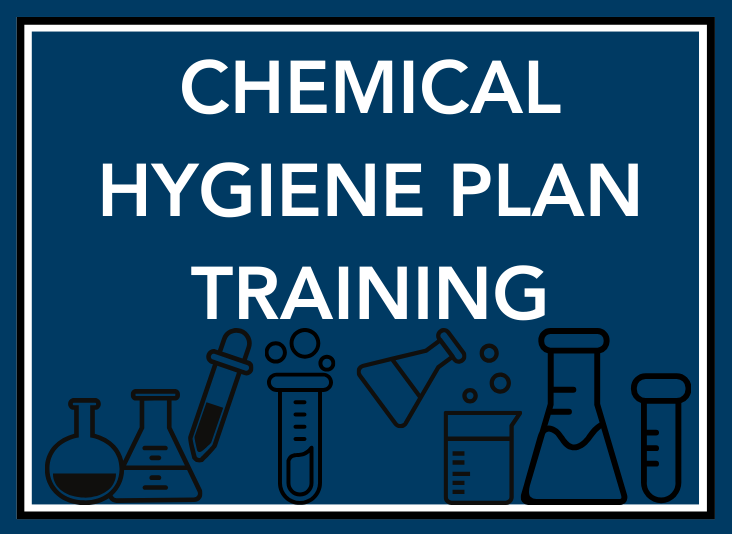
Laboratories generate chemical solvent waste every day. If mismanaged, this waste poses immense risk to staff, facilities, and operations—especially due to volatile organic compounds (VOCs) that are emitted from these chemicals.
Chemical Solvent Waste = Risk
Many common lab processes generate chemical solvent waste. Even minor direct or indirect interaction with these solvents can cause:
- Burning
- Vision loss
- Skin abrasion
- Organ failure
- And more
Direct solvent contact with clothing or skin often means immediate and obvious employee injury. There are also, however, less visible dangers from common lab wastes—when gaseous VOCs are generated.
Exposure to these harmful compounds—especially in labs and other enclosed areas where it is difficult for these gases to escape—can cause a number of long- and short-term health impacts to employees, including:
- Headaches
- Eye, nose, and throat irritation
- Nausea
- Liver, kidney, or central nervous system damage
- Memory impairment
- Cancer
Waste Mismanagement = MORE Risk
Common lab processes generate VOC-producing solvent wastes, including, but not limited to:
- High performance liquid chromatography (HPLC)
- Fast protein liquid chromatography (FPLC) with ÄKTA machines
- Ultra performance liquid chromatography (UPLC)
- Mass Spectrometry (MS)
Once chemical solvent waste is produced, poor waste management only increases employee risk—and emergency response calls. Besides employee risk, this can also mean:
- First responder injury
- Environmental damage
- Damage to brand reputation
- Loss of employee trust
- Financial loss
Solvent Waste Handling: Compliance Implications
Besides the safety risks they present, many existing solvent waste collection systems are in violation of the Resource Conservation and Recovery Act’s (RCRA’s) Title 40 regulations. RCRA 40 CFR 264.173 dictates specific hazardous waste collection guidelines; this RCRA regulation specifically states that: “A container holding hazardous waste must always be closed …”
But what exactly defines “closed”? The Environmental Protection Agency (EPA), which oversees RCRA compliance, defines “closed” based on specific parameters that vary based on the waste type. For liquid solvent wastes, a container is considered closed when “all openings or lids are properly and securely affixed to the container …”
Noncompliance with this specific RCRA regulation, and others, can mean:
- Fines of up to $90,702 per day
- Loss of brand reputation and damage to public image
- Employee distrust
Traditional Collection Methods
Traditionally, liquid solvent is collected in whatever container is available. Waste is funneled or tubed into a container placed near the workstation, with a funnel either attached to or resting on the opening. Unlidded bottles, broken caps, and flimsy containers may be used, with little regard for potential risk.
This method poses many problems, including:
- Collection with an open container. RCRA, satellite accumulation area (SAA), and OSHA worker safety standard regulations require all containers to be properly sealed. This avoids release of dangerous vapors.
- Containers placed on the floor can be easily knocked over; coupled with an open container, this could mean frequent spillage—which interrupts operations, causes lost valuable production time, and may mean extensive (and sometimes expensive!) cleanup.
- The lack of a filtration system means that VOCs and other harmful vapors are not captured before they can be emitted into the air.
Overall, this waste collection method doesn’t do away with the innate dangers of the chemical solvent waste. In fact, it increases the likelihood of spills and VOC emissions—and thus, introduces new and augmented risk to team members. Again, this means disruptions, loss of time and resource, and even noncompliance and citations.
Because of these immense risks, it’s up to environmental, health, and safety (EHS) managers to find a solution that will easily enable employee safety and organizational compliance.
Our System, Your Success
Safe, compliant, and efficient solvent waste collection is a challenge. Among the factors increasing complexity are:
- Closed container compliance logistics
- Exposure monitoring, if VOCs are or may be emitted
- Maintenance activities
Luckily, Triumvirate Environmental has extensive experience solving these issues—and has a solution called a VOCLok that helps mitigate these safety and compliance challenges.
To learn more about the VOCLok and how this system can work for you, read our Mini-Guide, view the product cutsheet, or contact us today.