EH&S: 5 Factors in Picking Out Hand Protection
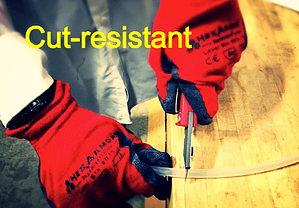
Last year, of all workplace injuries 23.2% of them were hand injuries. Of those hand injuries, cuts, punctures, or burns caused 15.1% of them. 70% of those who experienced workplace hand injuries were not wearing gloves.
When the correct hand protection is worn, it can reduce your chances of hand injury in the workplace by 60%. At least, that’s what Bill Soellner of Superior Glover Works and Larry Pricket of DuPont will tell you, just as they did in this webinar: “The Key Criteria for Glove Selection”. For your convenience, we’ve pulled the 5 key qualities to look for when picking out the perfect pair of gloves. Here they are.
Value
When picking out the right gloves, it’s important to consider value. This doesn’t mean the cheapest pair. You’re not saving money if a pair of gloves is half the price but only lasts a quarter as long. Valuable gloves are gloves that are durable and perform the functions you need them to perform. Gloves with an abrasion coating often last longer than those without.
Abrasion coating is a thin substance that coats and dries on a glove to protect it from wear and tear. The oldest kind of coating is latex, but many companies are now using synthetic blends that are stronger and less allergenic. Though these synthetic coatings last, solvents and oils make the coating sticky and soft.
When considering an abrasion coating, first consider what kind of work you’re going to be doing. Coatings also come in polyvinyl chloride (PVC), nitrile, and polyurethane.
Polyvinyl Chloride (PVC) is an inexpensive and versatile abrasion coating option. It’s abrasion resistant and good with water and detergents. It also helps keep workers’ hands dry. A drawback is that there’s no tactile feel to the gloves. This makes dealing with small objects or fine motor skills more difficult. It is however, an advantage when dealing with adhesives. I will address the advantages and disadvantages of other coatings in the following sections.
Thermal and Chemical Resistance
This is only important if you’re dealing with hot materials or chemicals. There are several standards used to measure protection against thermal contact. There’s the ANSI/ISEA standard that’s used in the US but has no regulatory body behind it and then there’s the EN standard used in Europe, which is used to make hand safety regulations there.
The ANSI/ISEA 105 measures conductive heat resistance and thermal properties based on benchmark temperatures and glove weight. It takes these into account and tests gloves based on factors like seconds to pain and seconds to second-degree burns. The glove is then bucketed into one of six performance levels. In other tests, the melt point or point of decomposition is also measured.
When it comes to chemical protection, gloves are tested based on permeation/breakthrough time on a scale of 1-6, the higher the number the more protection the glove will offer you.
Looking for higher levels based on either of these performance tests will help you find gloves with optimal protection. There are currently hundreds of blends and combinations of materials that are designed to protect during heat. Common materials for chemical resistant gloves include nitrile, neoprene, and PVC.
Laceration Protection
This is one of the most important factors when picking out a safety glove. Users want a glove designed to protect them against the type of laceration they are most prone to. Many users don’t realize that there are different kinds of lacerations that different materials work more efficiently against. Are you in danger of abrasions, punctures, cuts or all three?
Your answer will help you determine what material glove is best for you. ANSI/ISEA tests gloves on their efficiency in protecting against each type of laceration separately.
When it comes to cut resistance, knit gloves with coating are usually the best option. By knitting traditional fabrics (cotton, nylon, etc.) with thin strands of stronger materials (glass, steel, etc.) makers are able to make strong lightweight gloves.
The weight of the glove is also important in this situation. Typically, the heavier the weight, the stronger the glove will be against, cuts. This is, however, a give-take situation. Often times, the heavier the glove, the more difficult it is to move and work in the gloves.
Dexterity
This is huge for a lot of workers. A big reason workers don’t like to wear gloves is because they hinder their performance. Fortunately, innovations have been made to create materials that are ten times stronger than steel on an equal weight basis. This means you can find light, movable gloves that give you the level of safety you need.
One of the best materials for dexterity is polyurethane. It’ s stretchy and soft. Unfortunately, in heat (175 F) it starts to get sticky. There is some cut resistance but not as much as other materials. This material is best for dealing with solvents.
When considering dexterity, you should also take glove design into account. Do you need to work with your hands in tight spaces? Knitting without coating and Velcro straps are probably a bad decision because they can cause snagging.
Grip
Workers dealing with wet or oily substances often cite grip as a reason to not wear gloves: the gloves slip, making a job near impossible. Depending on the job and what’s being gripped, the solution may vary.
A common solution for wet or oily substances is a foamed nitrile abrasion coating. Nitrile is 3 times more puncture resistant than rubber, but has the capability of being foamed. When foamed nitrile is coated on a glove, the foam bubbles act as a sponge for the liquid substance and improve the grip of the glove.
To learn more about glove selection, check out this video we made!
For more info on best safety practices, contact our safety experts!